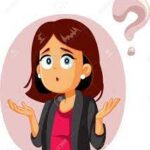
Incomplete Castings
There are a few reasons that castings do not fill completely. Look at your casting and see if the edges are rounded where the metal stopped flowing. If the metal is rounded it is probably one of two reasons. The metal was not hot enough.
Your metal casting temperature should be 100 degrees over the melting temperature. If you have to “eyeball” it, the metal should be shiny like mercury, rolling and active. If your using a torch to melt your metal, an easy way to see if it is ready to cast is to quickly pull the flame away from the metal for one second , if it clouds over, it is not ready, but if the metal stays shiny and active it is ready to cast.
Flask being too cool will also result in round edges on an incomplete casting. Your flask temperature should be 900 degrees for most castings. If you are casting delicate filigree type items the flask should be at least 1000 degrees when casting. If you are burning out at 1200 to 1300 degrees, let your flask drop down to the correct casting temp between 900-1000 degrees.
When you inspect an incomplete casting and it has jagged edges or holes with jagged edges, this usually indicates that your burnout was not complete. An easy way to tell if your flask is ready to cast is to look down the sprue holes and the sprue holes should be glowing red and there should be no dark spots in the holes. Investment should always be chalky white before casting and the sprue holes should be free of all residue. If you investment is grey, your burnout is not complete.
Improper sized sprues can cause incomplete castings. Sprues that are positioned incorrectley can cause incomplete castings. Make sure the diameter of the sprue is large enough to allow metal to easily flow into the casting. The position of the sprues also is very important.
Imagine a human standing with his (or her) arms to the sides. If you run a sprue to each foot, the metal flowing in the casting would have to go all the way up to the shoulders and then flow backwards down the arms to fill the hands. I would suggest running some smaller auxillary sprues to the hands to allow the metal to flow directly to that area of the casting insuring that the hands and fingers filled completely. Imagine the flow of the metal to all areas of your casting and add additional sprues to areas where the metal flow is not direct.
Porosity / Pitting
Too much heat can cause porosity and pitting in your casting. If you metal is smoking, you have overheated your metal. Again, the casting temperature is 100 degrees over the melting temperature.
Another culprit causing porosity and pitting is using dirty metal. It is so important to use clean metal when casting.
Always make sure your sprues are clean and smooth. A hole in a sprue or gaps in your spruing will let investment fill into the gap or hole. When the wax is burned out, you are left with a piece of investment standing in the way of the metal as it flows into the cavity and can break off and mix into your metal causing a nasty pit.
All that being said, many time you can flow solder into a pit or porosity and then finish out the casting instead of recasting the item.
Bubbles
Bubbles Bubbles toil and troubles. Don’t you hate having a casting covered in bubbles? Bubbles are created when you mix your investment. A thinly mixed investment will cause tiny bubbles, a very thick investment will cause large bubbles. A perfectly mixed investment will cause bubbles unless you remove the bubbles from your investment or shake them loose from your wax patterns during the investing process. We suggest using a vacuum investing system. You will mix your investment in a bowl and then vacuum the investment in the bowl for about 90 seconds before pouring your investment into the flask. Then you should vacuum the flask for another 90 seconds. Then follow up by placing the flask on a vibrating table for 30 seconds, or gently “swirling” the flask by hand to help release any remaining bubbles. You need at least 30lbs of vacuum pull when investing your bowl and flask.
If you cannot afford a vacuum investing system, then at least get a vibrator to release the bubbles from the wax. There are also products available at your local jewelry supply store that you paint, spray or dip your wax pattern into before investing. These products reduce the “surface tension” that holds the bubbles onto the wax and helps release the bubbles when the investment is poured around the wax pattern.
If you live in an area that is very cold in the winter, your water from your faucet will be much colder in the winter than in the summer. Investment mixed in warm water will set up faster than investment mixed in cold water. Your investment to water ratio should always be the same and the water temperature you invest with should always be the same to insure consistent results. Use 68 degree water if possible, summer and winter and your investment will act the same all the time. This will help you get the exact results you need.
Bubbles can also be caused by using an old box or bag of investment. We used to buy investment by the ton, sometimes when we got down to the last few boxes, we would start getting bubble problems in our castings. Even though we were doing everything exactly the same. We finally figured out that the bubbles were caused when we used the older boxes of investment. Changing to a new fresh batch of investment cleared up the bubble problems. There is usually a date code on the box of investment that will let you know how “fresh” the investment is. Don’t buy investment that has been sitting at the jewelry supply store for several months. If you do need to use old investment, roll the box around on the floor before using to help mix the ingredients up, that will help.
Blow Outs / Cracked Investment
Blow Outs can happen with Vacuum or Centrifugal Machines. Your metal is spun out or sucked out of the flask and can cause damage to your machine, or to you by hot metal going where it is not supposed to go. It can be very dangerous and expensive. Blowouts occur because the investment is mixed too thin or the waxes are too close to the end of the flask. Always have at least 1/2 inch of investment between your last wax pattern and the end of the flask and always mix your investment correctly. Investment will also break down at higher temperatures and can cause cracks in your investment which again can lead to a blow out or “flashing” of the castings.
Make sure your investment sets up for a minimum of one hour, we always do two hours to be safe. Do not put flasks into a hot oven, it is a disaster waiting to happen. Slowly bring your oven to 1100 to 1200 degrees.
Vacuum Casting VS Centrifugal Casting Machines
Unless you are buying a very expensive induction system (vacuum) we suggest using a centrifugal casting machine. You will save yourself a lot of headaches. Centrifugal machines are more forgiving, less overall problems. Just my opinion.
Advice When Casting
Have you heard that old adage, “There is never enough time to do it right, but there is always time to do it again”?
Don’t rush the casting process. You can crank your oven up on high and burn out in 45 minutes. You can let your investment set up for 45 minutes instead of 1-2 hours. You can turn up your melting furnace or torch and melt the metal in 1/2 the time. You can get away with it some of the time. But at what results? Cracked Investment, Blowouts, Bubbles, Pitting & Porosity, wasted time and money. The best advice I can give is, Take your time and do it right the first time.
If this page did not address a problem you are having with your castings, email us at [email protected] and we will do our best to help you out. Thanks so much and Happy Casting!